Six Sigma
Six Sigma is a disciplined, data-driven approach to quality management that aims to minimize defects and variability in processes, products, and services. It is a methodology that was first introduced by Motorola in the 1980s and has since been widely adopted by many organizations in various industries.
The name “Six Sigma” refers to a statistical measure of quality that represents the number of defects per million opportunities. The goal of Six Sigma is to achieve a level of quality that has no more than 3.4 defects per million opportunities, which is equivalent to a Six Sigma level of quality.
The Six Sigma methodology is based on a five-step process known as DMAIC, which stands for Define, Measure, Analyze, Improve, and Control. The DMAIC process involves the following:
Define: Identify the problem, goals, and objectives of the project.
Measure: Collect data and measure the current performance of the process.
Analyze: Analyze the data and identify the root causes of the problems.
Improve: Implement solutions to address the root causes and improve the process.
Control: Establish controls and monitoring systems to ensure that the improvements are sustained.
The Six Sigma methodology uses a variety of statistical tools and techniques, including process mapping, statistical process control, design of experiments, and hypothesis testing, to identify and eliminate defects and variability in processes.
The benefits of implementing Six Sigma include improved quality and customer satisfaction, increased efficiency and productivity, reduced costs and waste, and increased profitability. Six Sigma also helps organizations to establish a culture of continuous improvement and achieve long-term success.
Six Sigma for process Improvement
Six Sigma is widely used for process improvement across many industries, including manufacturing, healthcare, finance, and services. The DMAIC process, which is the core of Six Sigma methodology, provides a systematic approach for improving existing processes or developing new ones.
The first step in using Six Sigma for process improvement is to identify the process that needs improvement and define the problem or opportunity. This involves gathering data and input from various stakeholders, including customers, employees, and other stakeholders.
Once the problem has been defined, the next step is to measure the current process performance using metrics and data. This involves collecting and analyzing data on the process, such as cycle time, defect rate, and other performance indicators.
The third step is to analyze the data to identify the root causes of the problems or opportunities for improvement. This involves using statistical tools and techniques to analyze the data and identify patterns and trends.
Based on the analysis, the team can develop and implement solutions to improve the process. The solutions should be tested and refined to ensure that they are effective and sustainable.
The final step is to establish control measures to ensure that the improvements are sustained over time. This involves monitoring the process performance and implementing corrective actions when necessary.
Overall, Six Sigma provides a structured approach for process improvement that is based on data and facts, and is aimed at reducing variability and improving quality. By implementing Six Sigma, organizations can achieve significant improvements in process performance, customer satisfaction, and profitability.
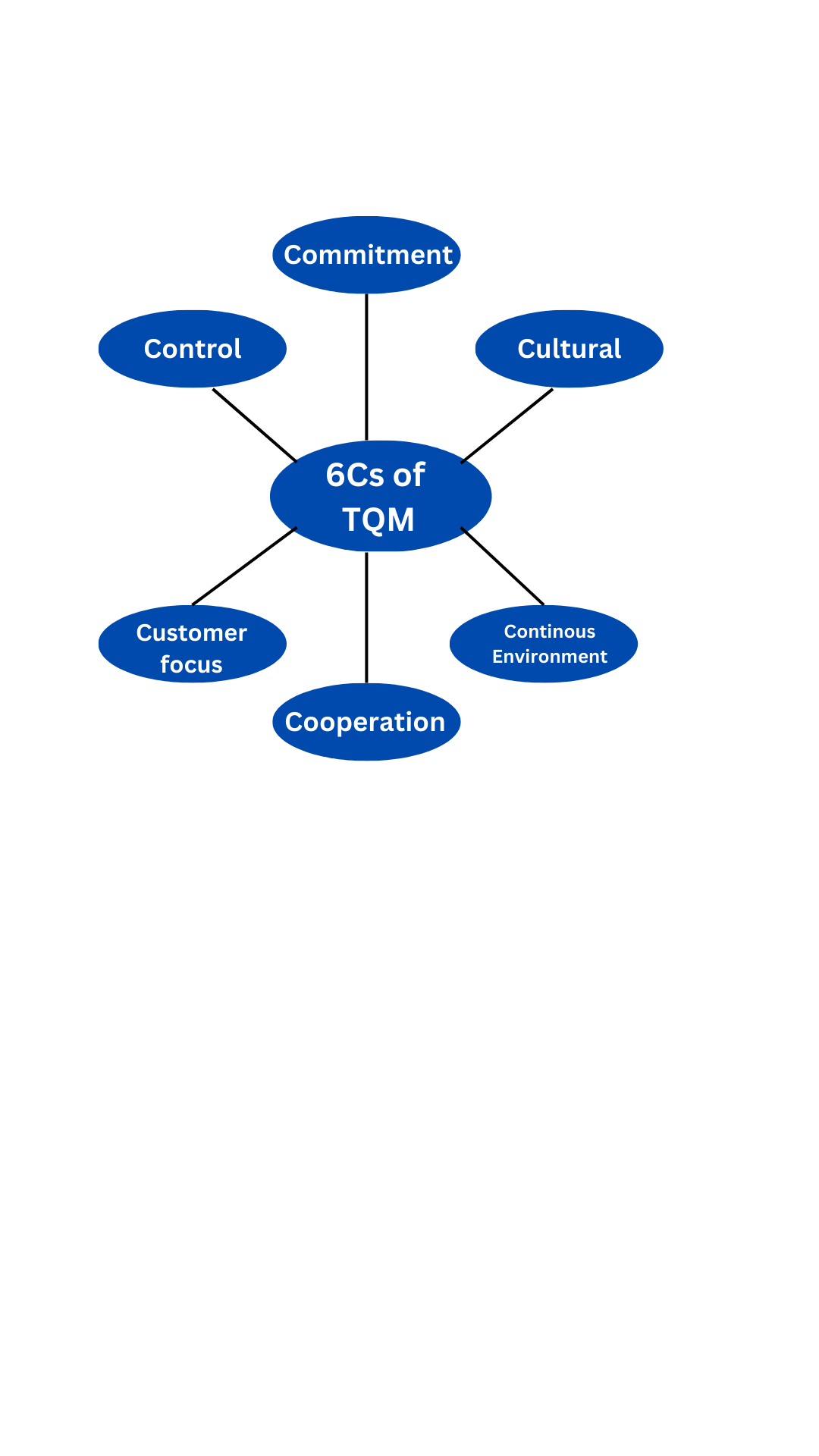